|
EOSTD_CYL SERISI KARTUSLU ETILEN OKSIT GAZ STERILIZA TÖRLERI
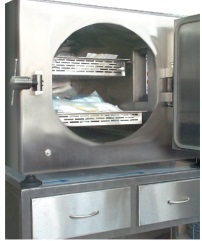
A. DESCRIPTION OF THE DEVICE
The devices have been developed in a way that they can be sterilized by using disposable cartridges containing 100% ethylene oxide gas for both cold and sanitary sterilization. For one sterilization the EOSTD_CYL 160 model uses a single 134 gm cartridge. The sterilization process takes place at 37 ° C, 55 ° C. This selection is made by the user with the touch keys on the control panel. In addition, there is a "user-defined program" option that can be programmed by the user, apart from the above standard values ??for the sterilization temperature and time.
With this option, between 35 C and 55 C
sterilization at any temperature
Sterilization cabin has a CYLINDRICAL structure and its volume; For EOSTD _CYL 160 is 160 liters. Cabin
The dimensions are; Diameter: 45 cm, Depth: 101 cm.
In EOSTD_CYL 160 series devices, the sterilization cabinet can also be used as a ventilation cabinet. The devices perform ethylene oxide sterilization in four phases. These phases are respectively; CONDITIONING PHASE, STERILIZATION PHASE (exposure), GAS TIMELINE PHASE (exhaust) and
VENTILATION IS PHASE. Excluding the aeration phase, the total sterilization time is at 37 C when a 134 gm cartridge is used; If 6.5 SAA T 'is at 55 C; 4 is SAA T. In user-defined programs, the temperature can be adjusted between 35 C and 55 C at the desired value.
The duration of the ventilation phase can be selected by the user between 0 and 99 hours. The ventilation process is carried out by washing with warm air in order to ensure that the very small amount of gas that is likely to remain in the packaging of the sterilized materials is completely diffused out in a short time.
During this process, the air taken into the environment is passed through a bacteria-retaining "HEP A" filter and taken into the cabinet. All functional processes such as the pressure, humidity, temperature conditions required for sterilization and the gas in the cabinet by piercing the cartridge placed in the chamber after the conditioning phase, an electronic information It is performed completely automatically by the processing unit and is kept under control during sterilization. All functional operations of the device and error messages are written down with the help of a recorder. The device stops automatically after the sterilization and ventilation processes are finished and warns the user visually and audibly. The inner surfaces of the sterilization cabin and the cover system of the device are completely made of quality stainless steel. Check whether the lid is securely closed before sterilization begins.
a message indicating that it appears on the function screen. There is a magnetic lock system that prevents the lid from opening during the sterilization process. The device operates under negative pressure throughout the sterilization process. Device pressure tests are performed at 5.5 Atu hydraulic pressure. EOSTD_CYL 160 model ethylene oxide gas sterilizers
A unit developed by our company has been added to the devices in order to continue the operation safely from where it left off, taking into account the power failure or malfunctions that may occur in the network. Thanks to this system, without emptying the device and refueling new gas and
Sterilization can be completed without wasting time.
In case the cover is not closed completely, the device will not accept the start command and an audible warning will be heard.
A chemical neutralization system is used in the devices in order to prevent the gas to be expelled during the gas discharge from damaging the environment. Thanks to this system, the harmful toxic effect of ethylene oxide gas is eliminated and its ejection is ensured. The vacuum pump, which performs vacuum, gas evacuation and ventilation processes, is located in the device anchorage.
External dimensions of the device (approximate): Width: 90 cm
Height: 136 cm
Depth: 130 cm.
WORKING PRINCIPLES:
EOSTD_CYL 160 model ethylene oxide gas sterilization devices perform the sterilization process at two different standard temperatures (37 C, 55 C) that the user can choose or at any value between 35 C - 55 C given in user-defined programs and in four basic phases. These phases are respectively:
1) Preparation phase (conditioning):
In this phase, the device creates an environment that can optimize the sterilization capability of ethylene oxide gas inside the cabinet. As the operations performed;
i) V acum (-0.7 bar),
ii) Preheating (35 C - 55 C according to the selected value),
iii) Humidification (~ 35-50% RH)
2) Sterilization (exposure) phase:
The sterilization process starts with the automatic piercing of the gas cartridge placed in its slot in the cabinet and taking the ethylene oxide gas into the cabinet. When entering the cabin, the cooled gas is brought back to the cabin temperature. When the cabinet and gas temperature reach the set value, the sterilization process starts.
3) Gas discharge phase (exhaust): The gas in the cabin as a result of the sterilization process is absorbed by vacuum and neutralized by washing with water.
It is given to the drain. The vacuum process takes about 5 minutes. This process can be repeated 5 times, depending on the user's request. If the ventilation time is to be kept short, the vacuum process should be repeated more than once.
4) Ventilation phase: Following the degassing phase, the very small amount of ethylene oxide gas remaining in the package is completely destroyed by washing with 1 Atu pressurized warm air that lasts 0 - 99 hours. This process can also be done in a separate ventilation cabinet.
EOSTD_CYL 160 model ethylene oxide gas sterilizers work with the help of an 8 bit microprocessor controlled process control unit. With the help of the alphanumeric indicator on the control panel, parameters such as sterilization phases, temperature, pressure, time and error messages can be monitored continuously. In addition, a printer located on the control panel writes the parameters and messages on paper. The device has a reservoir where the water required for moistening process is supplied. This tank reserves 10 sterilized water (~ 1.5 liters). When the water runs out, the user is warned in writing and audible on the screen and the device does not receive a start command. Heating of the cabin is provided with the help of film heaters located on the outer wall of the cabin (6 surfaces including the cover). Thermal insulation is made with 80 mm thick aluminum foil glass fiber.
FUNCTIONAL UNITS
1. RECORDER
2. MANOMETER (CABIN)
3. ON-OFF BUT KEY
4. ELECTRONIC CONTROL AND CONTROL UNIT
5. HEAT CONTROL ELECTRONIC CARD
6. FEED TRANSFORMER
7. INPUT-OUTPUT-INTERF ACE CARD
8.STEAM GENERA TORU SAFETY VALVE
9.VACUUM SYSTEM COMPRESSOR
10. HUMIDIFYING STEAM GENERA TOR
11. STEAM GENERA TORÜ HEATER
12. VACUUM SYSTEM BY -PASS VALVE
13. MAINS WATER INLET
14. DISCHARGE
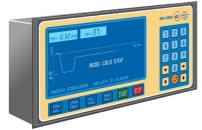
D. ELECTRONIC STRUCTURE
p>There is an information processing unit in the device, which performs all commands and controls, and includes microprocessor and peripheral equipment. Parameters such as temperature, humidity, pressure, and the status of functional units from the sensors are evaluated in this unit and the sterilization process is carried out with the commands generated by this unit according to the selected sterilization type. INTEL based OTP type CPU (central processing unit) is used in the micro-processor card. There is a back-up system that can keep the program parameters in memory for 10 years. There is an LED indicator that shows the pressure and temperature continuously and an alpha-numeric GRAPHIC LCD display showing sterilization functions, program parameters and error messages. Values ??such as program parameters, time and date are entered via numerical keys on the information processing unit. The information processing unit commands are sent to the micro-processor based input-output control card in the control unit via serial communication method, enabling functional units such as pumps, heaters and magnetic valves to be operated. In addition, the data processing unit prints the sterilization stages, parameters and error messages to the thermal recorder, also via serial communication method.
|